Turbomachinery
The use of ML in turbomachinery speeds up and optimizes your design workflow
Turbomachinery
Problems
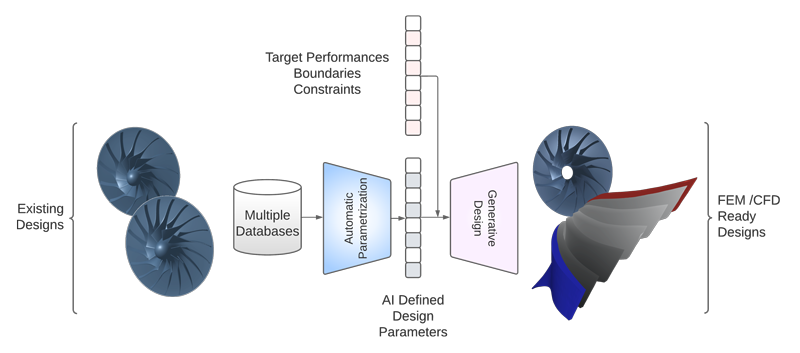
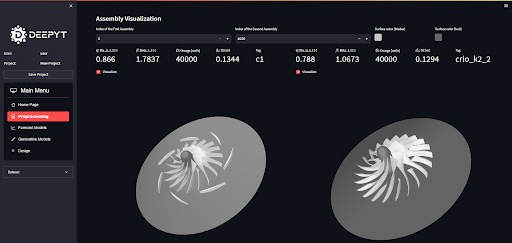
Aerodynamic design of turbomachines is a complex and interesting process. This involves a preliminary 1D analysis, moving on to a 2D meridional and blade to blade analysis and to a 3D CFD geometry that will be optimized.
During design, a great deal of input is required from the designer due to his experience and ability to improve the product.
Design is an iterative process, during which a large amount of data is produced. Most of these will be discarded and forgotten once the final product design is achieved.
Aerodynamic design based on numerical and experimental simulation generates a large amount of data, in complex formats that are difficult to interpret (individual performances, field quantities, time series, 3D geometries, etc.).
Exploring this data to derive useful information for current and future designs is a great challenge.
To develop a new product, it is typically necessary to start from scratch, without exploiting previous know-how, with consequences in terms of time and costs.
CFD and FEA calculations can be problematic from the point of view of computational weight and simulation time, limiting the number of solutions analyzed in the design and optimization phase.
Parameterization is based on parameters manually defined by the designer and for this reason are typically a limited number of macroscopic geometrical parameters.
The use of Engineering Design Parameters (EDPs) requires a uniform parameterization of each case study to obtain uniform tabulated data that can be used for analysis, possibly requiring reparameterization of the available geometries
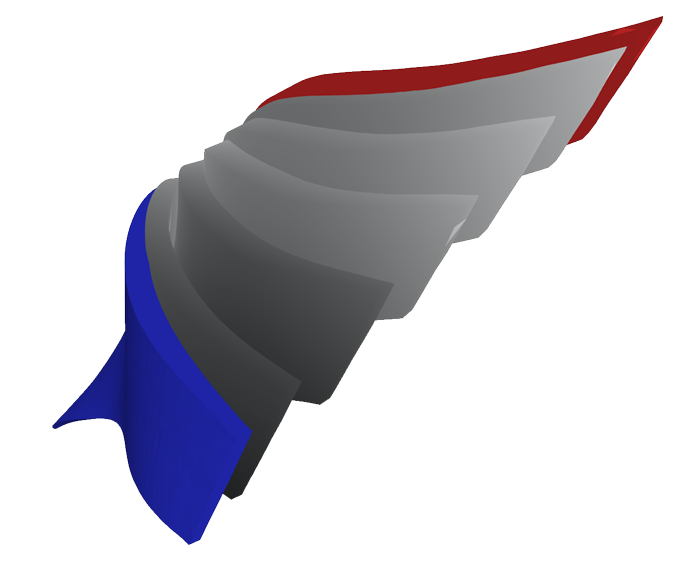
Our Approach
Main Concept
- Collecting data from the company’s history or from available simulation tools
- Implementation of the preprocessing chain
- Automatic parameterization of geometries with artificial intelligence algorithms
- Performance forecasting of existing and new designs
- Generation of new geometries ready for simulation based on performances specifications
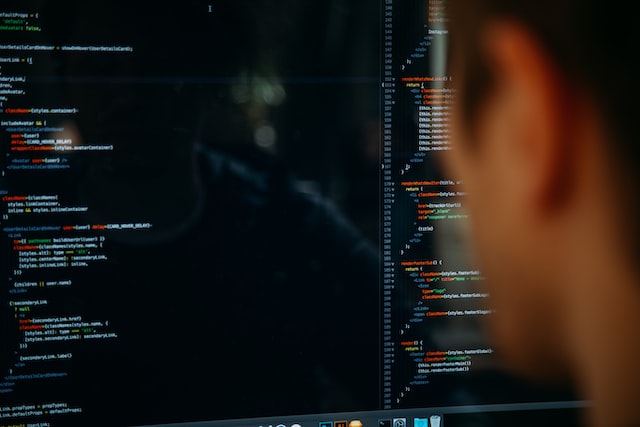
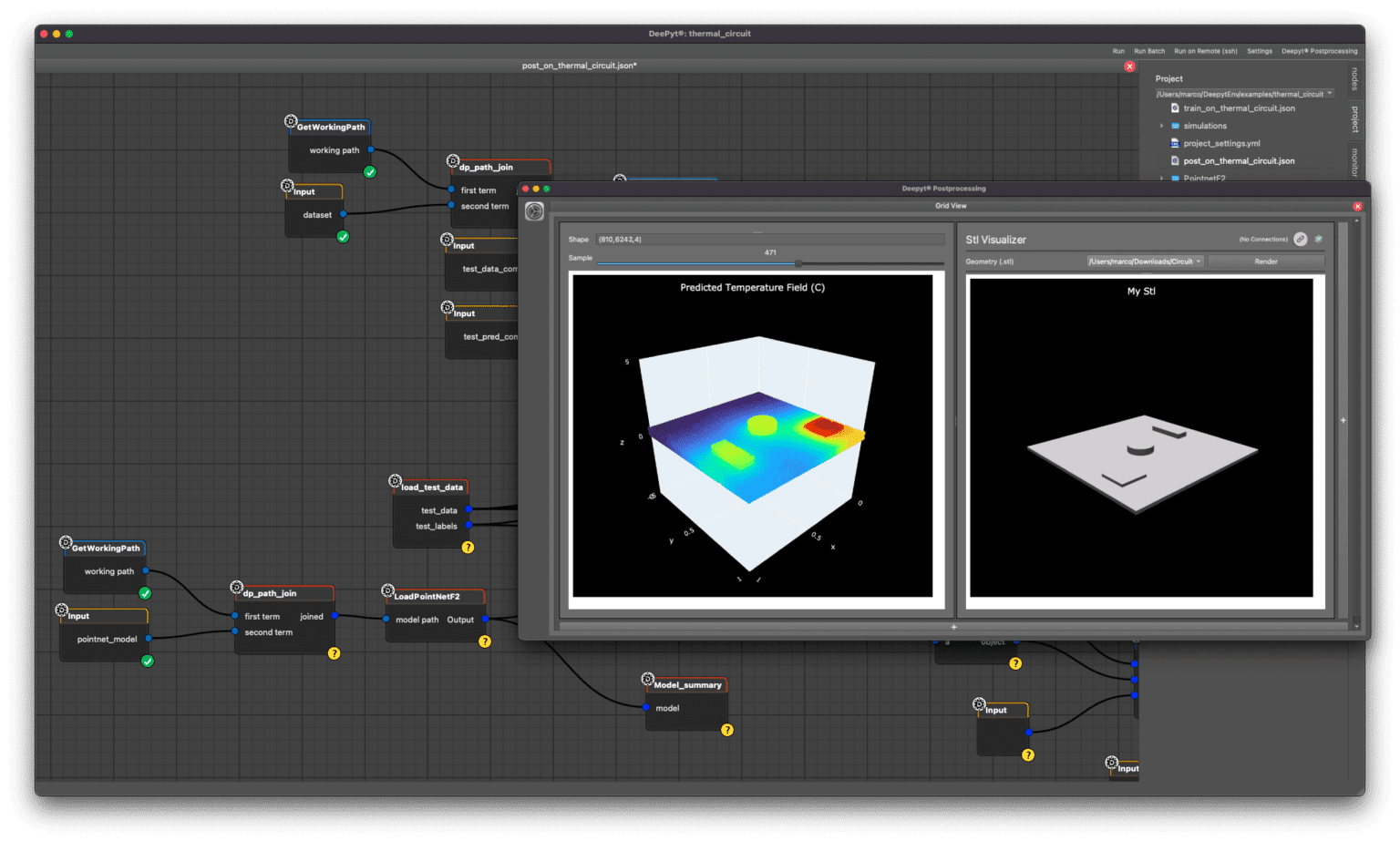
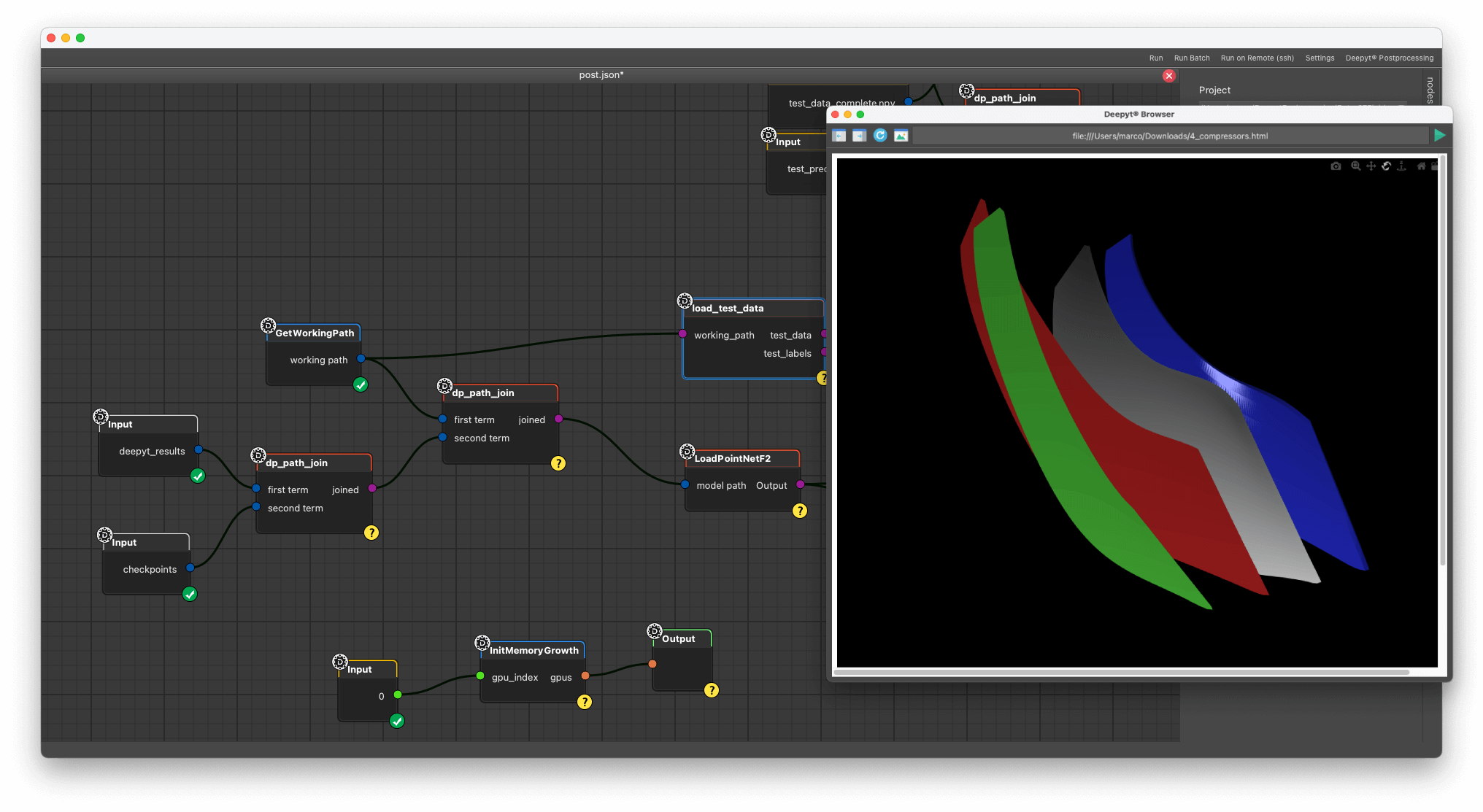
Exploiting your data
Deepyt uses your historical or experimental data from previous datasets and design cycles.
You can export your simulation data (FEA or CFD) and load it directly into Deepyt, using the raw CAD itself or tabular data.
Artificial intelligence algorithms that can be developed with Deepyt make it possible to process all this data and automatically extract a large amount of information, which can be exploited for one’s own purposes.
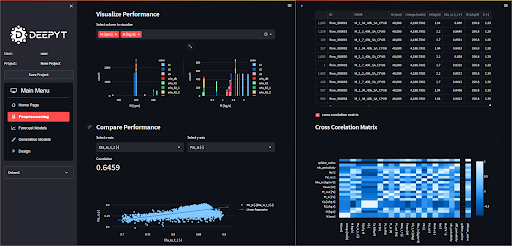
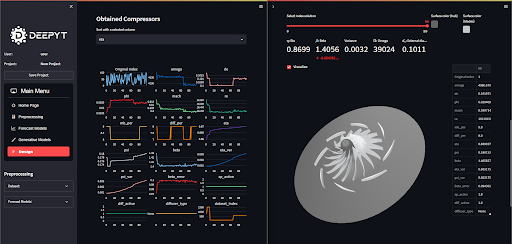
Don't waste knowledge
Using your past projects to develop artificial intelligence algorithms means keeping track of the expertise provided by the designers who contributed to the product design.
Several projects can be analyzed at the same time, extracting all available information, giving value to past experience.
Speeding up design
With our algorithms, it is possible to forecast fluid dynamic/structural performance from pure 3D geometries, tabular data, time series or combinations thereof.
This makes it possible to instantly verify the performance of new designs.
You can build forecasting machine learning models and train them on your performance data, you will be able to exploit the metamodel to predict field quantities on surfaces and volumes for new geometries with a very high accuracy, speeding up the design process!
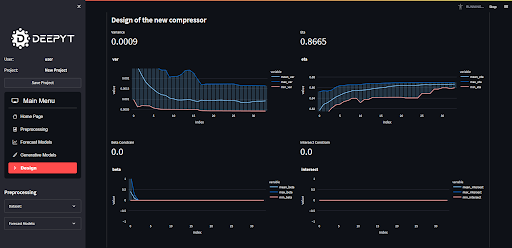

Automatic parameterization
Our advanced autoencoders automatically convert and compress your 3D designs into a set of latent parameters, that can be used for subsequent design or optimization.
Optimization
For a known target performance, the autoencoder can provide the parameters for the performance-optimized 3D design and even rebuild your geometry in a ready to export format, reducing the number of simulations required to achieve peak performance.
With our technology it is possible to have a clean CAD that can be automatically meshed and evaluated through CFD or FEM, it is an automatic optimization based on non-parameterized geometries!
Working on latent parameters, it is possible the exploration of design space that is difficult to exploit with traditional parameters optimization.
Reinforcement learning is one of three basic machine learning paradigms, alongside supervised learning and unsupervised learning. With this approach, the algorithm learns on its own by repeatedly failing to perform a desired task.
These algorithms, coupled with generative design and accurate performance forecasting algorithms, represent an effective and innovative design solution.
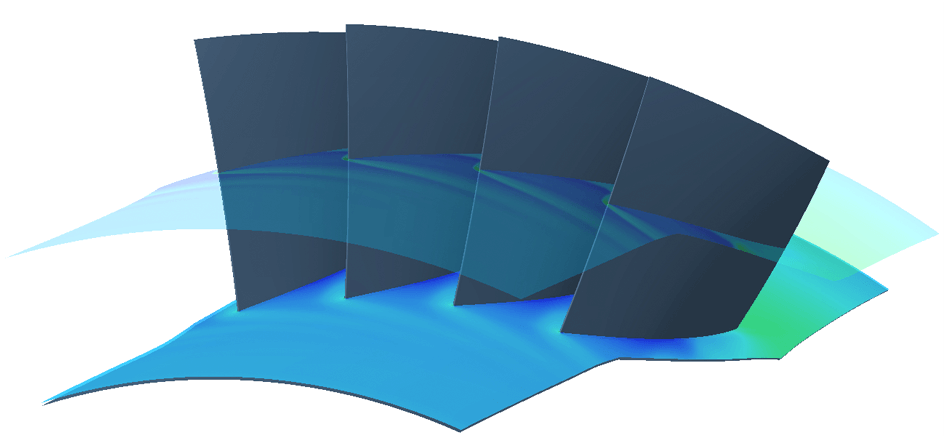
Original
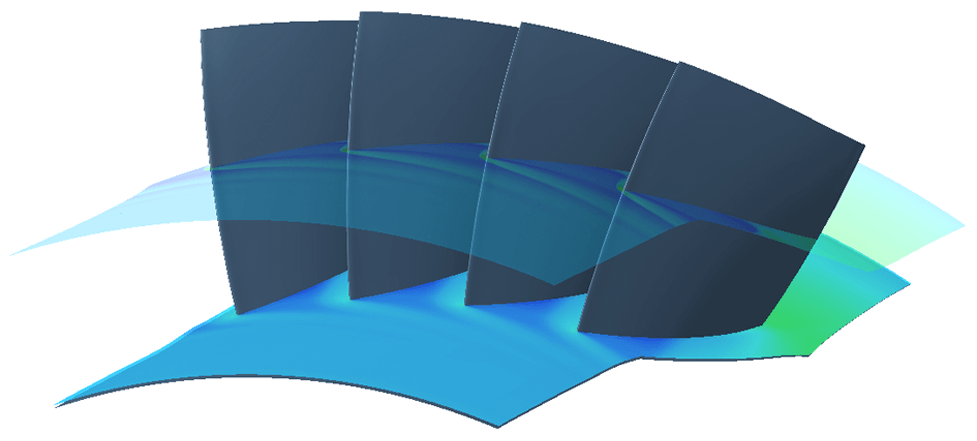
AI Generated
Generative Design
With the use of algorithms such as Variational Autoencoders or GAN (Generative Adversial Networks), completely new geometries can be generated, developing a new 3D geometry according to specifications.
The accuracy of the reconstruction can be such that the geometry can be directly verified with fluid dynamic and structural calculations.
Ready-to-go examples
Thanks to the available and downloadable library of ready-made projects, it is possible to experiment with the algorithms in just a few minutes and visualize the results.
Adapt the examples to your case study and use our algorithms for your application.
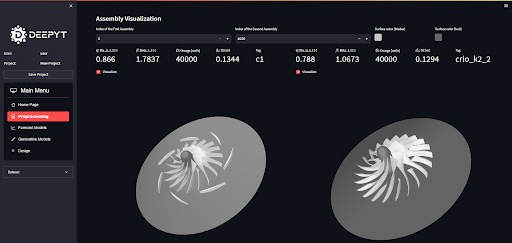